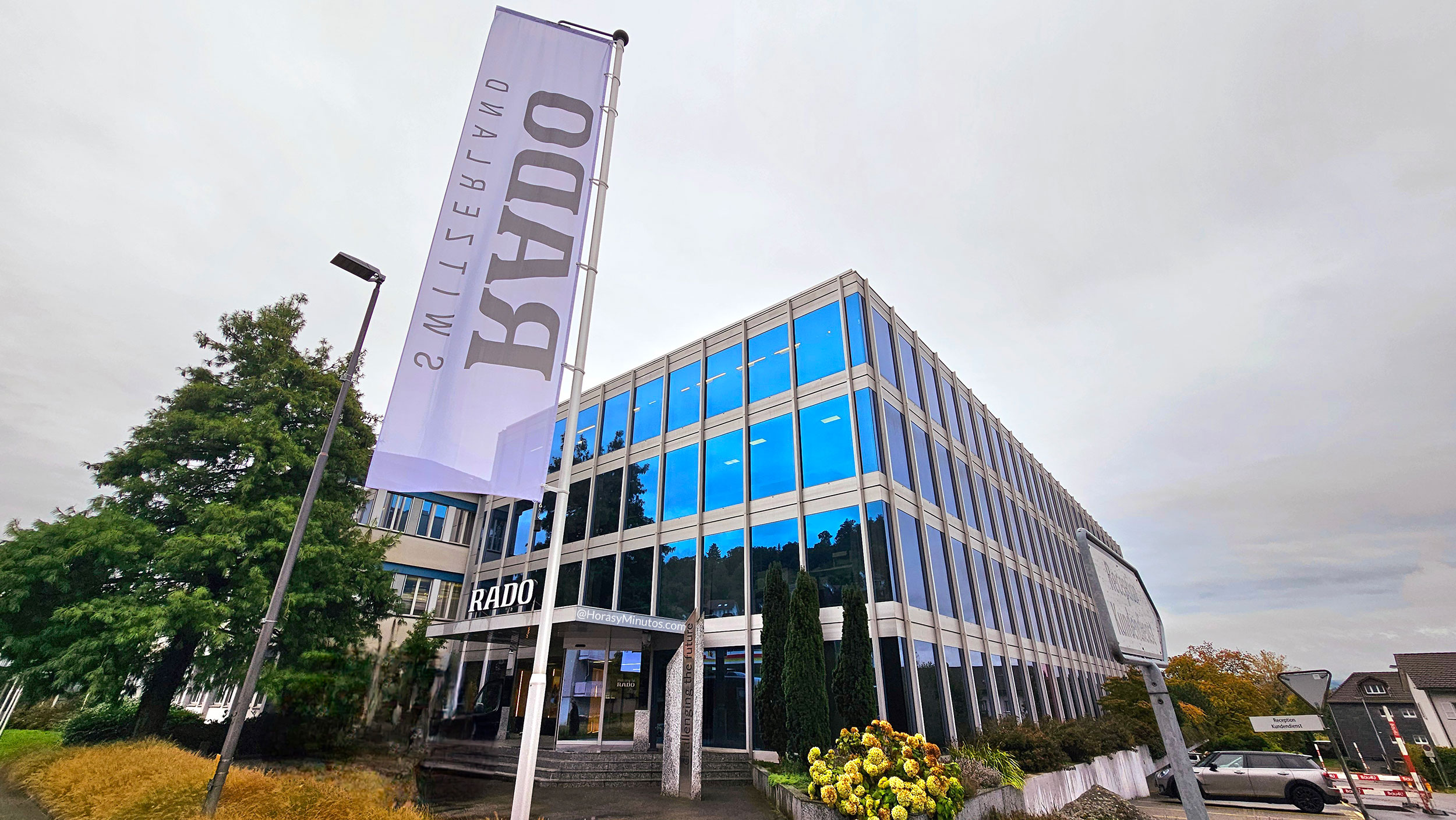
Hay casas relojeras que se remontan a los primeros tiempos de la relojería. Me refiero a aquellas que sienten predilección por el guilloché ornamentado, los calendarios perpetuos y los repetidores de minutos. Y no tenemos nada en contra, por supuesto. Nos encantan. Sin embargo, algunos de los nombres más importantes del sector no son los que se aferran a ese legado centenario de relojes de lujo hechos a mano. De hecho, en algunos casos se podría argumentar justo lo contrario. Una de esos casos es el de Rado, conocida como «Maestro de los Materiales», y yo he tenido la suerte de visitar su base de operaciones.
La industria relojera en general no cambia a menudo. Es más de cambios graduales que de movimientos sísmicos. Pero sí cambia y Rado ha sido, desde 1917, una parte vital de ese cambio. Sí, Rado. Desde una perspectiva externa, podría parecer raro que una marca tan poco habitual en las cabeceras de noticias relojeras haya influido directamente en ciertos aspectos de la relojería, pero, en un sentido (muy real, dada su historia), su declaración de principios ha llevado el diseño y los materiales más allá de lo que lo habrían hecho otras marcas. ¿Su misión? «Si podemos imaginarlo, podemos hacerlo. Y si podemos hacerlo, ¡lo haremos!». No se puede tener un lema más positivo y de futuro que ese, ¿verdad?
UN POCO DE HISTORIA
Rado nació como Schlup & Co., una prueba más de que, a veces, el nombre familiar no es el más comercial que se puede elegir. Fue fundada en 1917 por los hermanos Fritz, Ernst y Werner Schlup, que de hecho convirtieron la casa de sus padres en su taller relojero. Si cuando eres padre estás deseando que tus hijos se vayan de casa, imagínate cómo se sintieron los Schlups cuando vieron su hogar convertido en fábrica (incluso me parece oír a la madre: «¡pero mira cómo me tenéis todo, manga por hombro!»).
Sea como fuere, los hijos no eran los clásicos vástagos que se dedica a vaguear por casa a la espera de triunfar en YouTube. Muy al contrario: los hermanos tenían un don para los negocios. Durante los primeros años fue una fábrica de relojes que producía movimientos de áncora de cuerda manual, pero gracias al trabajo en equipo y después a la creciente demanda militar, unida a su innata calidad suiza, el fabricante Schlup creció a un ritmo asombroso hasta que, al final de la Segunda Guerra Mundial, era uno de los más grandes del país. Esto significaba, por supuesto, que había llegado el momento de capitalizar ese éxito con un nombre: Rado, que en esperanto significa «rueda», un elemento básico en la estructura mecánica de un reloj.
La empresa se centró en la producción de relojes acabados en lugar de movimientos ébauche, a raíz de un cambio drástico en la demanda. Uno de los primeros modelos es el Golden Horse, presentado en 1957 y resucitado en 2019 (aquí vimos en vivo la preciosa reedición).
Fue sin duda un caballo ganador (o caballito, deberíamos decir si nos fijamos en su símbolo), gracias a una combinación de diseño sin fisuras y su resistencia al agua, algo no muy cuidado en aquel entonces en relojes de diario. Pero los verdaderos fuegos artificiales llegaron un poco más tarde con uno de los relojes más influyentes de la década de 1960, el Rado DiaStar 1 (un 1 que perdió según se desarrolló su historia). Un reloj que se sigue vendiendo en grandes cantidades hoy en día, sin ningún tipo de publicidad (como curiosidad, Pelé tuvo un par de ellos).
El lanzamiento del Diastar en 1962 fue todo lo que los demás relojes no eran. Rado lo promocionó como «el primer reloj del mundo a prueba de arañazos», y también uno de los primeros en utilizar zafiro para su cristal en lugar del mineral, que era más común en aquella época. La caja y el brazalete eran de carburo de wolframio (llamado «hardmetal»), que no era una cerámica pura, sino un híbrido de metal y cerámica (también conocido como «compuesto de matriz metálica»), que mezcla elementos de wolframio y carbono y tiene muchas propiedades metálicas. Se utiliza mucho en la fabricación de productos como brocas y herramientas quirúrgicas, pero era un material raro de encontrar en un reloj de pulsera, y más en la década de 1960. Incluso en estos tiempos relojeros, a decir verdad.
Además, las formas del reloj resultaban muy novedosas entonces, y aún lo son hoy en día. Aquí conté su historia, además de ver en vivo los últimos modelos.
El DiaStar sentó las bases para futuros desarrollos en el campo de la cerámica, definida de forma genérica como un material duro, quebradizo, resistente al calor y a la corrosión, fabricado a partir de la cocción de un material inorgánico no metálico a altas temperaturas. Aunque, como veremos, el proceso no tiene nada de genérico y sí mucho de tecnológicamente avanzado.
En 1962 también se lanzó el RADO Captain Cook. Su vida no fue tan exitosa en su momento, porque sólo se fabricó seis años. El reloj tuvo que esperar hasta 2017 para un renacimiento que, esta vez sí, ha sido bendecido con el éxito entre los aficionados que el modelo se merecía.
En este vídeo presenté los nuevos modelos de 2017. Desde entonces han sido innumerables las variaciones, que demuestran la buena salud del buzo de la casa.
En 1983 nació el RADO Anatom. Con este reloj, el relojero suizo llevó su anterior afición por las formas rectangulares y los avances tecnológicos al siguiente nivel. Incluso el nombre ya lo sugiere: Anatom se compone de «atómico», en alusión a su diseño futurista, y «anatómico». Esta última atribución apunta a la ambición de Rado de crear un reloj que, gracias a su forma convexa y su cristal de zafiro hecho a medida, se amoldara anatómicamente a la muñeca y ofreciera así un alto nivel de comodidad al llevarlo.
Aquí está el modelo original y el actual de 2024:
Y aquí está el vídeo donde analizo la versión moderna del Anatom:
A mediados de la década de 1980, Rado volvió a innovar en el campo de los materiales con el Integral, un reloj rectangular con brazalete de cerámica, el primero del mercado.
Con el lanzamiento del Integral, Rado comienza a trabajar con cajas de cerámica de alta tecnología. Son resistentes a los arañazos, ligeras y tienen una superficie lisa. Cuatro años más tarde, Rado intensificó el uso de la cerámica de alta tecnología y lanzó el Ceramica en 1990. No sólo los eslabones del brazalete eran de cerámica negra, sino también la caja y la corona. El Ceramica es, probablemente, el reloj en el que más se piensa cuando se habla de Rado. O por lo menos hasta la reintroducción del Captain Cook, que se ha convertido en la estrella de la casa.
Como hasta entonces los relojes de cerámica sólo estaban disponibles en negro, Rado lanzó el White Coupole en 1992. Fue el primer reloj de pulsera del repertorio de Rado fabricado en cerámica blanca de alta tecnología. En los años siguientes, Rado amplió continuamente la paleta de colores de sus relojes de pulsera de cerámica añadiendo pigmentos: en la actualidad, son posibles unos 20 colores.
Rado también experimentó con combinaciones de cerámica de alta tecnología con otros materiales. El Sintra de 1993, por ejemplo, era una fusión de cerámica de alta tecnología y metal, una combinación que más tarde se llamaría Ceramos.
Poco antes del comienzo del nuevo milenio, en 1998, Rado demostró que la cerámica puede brillar como el metal con el lanzamiento del Plasma Metallic Grey Ceramica. El aspecto metálico de esta cerámica se consigue mediante un tratamiento con plasma. Tanto por el Ceramica como por el Sintra, Rado ha sido galardonada por sus innovaciones tecnológicas en concursos de diseño.
Y toda esa mágica mezcla de materiales, calor y relojería se lleva a cabo dentro de Comadur, la fábrica de materiales de alta tecnología del Grupo Swatch que, con toda la lógica, está integrada en el edificio de Rado.
DENTRO DEL LABORATORIO
Visitar Comadur es como entrar en el taller de un alquimista, donde ves un montón de materiales sueltos que no parecen casar juntos, pero que se terminan conviritiendo en los relojes de Rado.
Comadur se fundó el 1 de enero de 1984 tras la fusión de las empresas Seitz & Co, Méroz Pierres SA, Sadem SA, Romelli, Rüfenacht y Watch Stones & Co SA, a su vez también resultado de una serie de fusiones.
El nombre de la empresa es un acrónimo de «Composants en Matériaux Durs» (componentes de materiales duros). Esto pone de relieve su implicación activa en varios sectores asociados, como los cristales sintéticos (zafiro, rubí, etc.), la cerámica (alúmina, circonio, nitruros, carburos, etc.) y las tecnologías de producción de polvos de tierras raras (polirubíes, microimanes, etc.).
Estos son los materiales con los que trabaja y sus propiedades (en lo que nos interesa, hay que fijarse en la escala de dureza Vikers):
Las aplicaciones de los productos de Comadur están relacionadas con la microtecnología, principalmente para la relojería, pero también para otros sectores como la medicina, la óptica, la industria aeroespacial, la telefonía, la hidráulica, la electrónica, los bienes de consumo, etc.
Una de las primeras cosas que hay que entender sobre la producción de componentes cerámicos para relojes es que es mucho más compleja que la de materiales convencionales como el acero, el oro, el bronce o incluso el titanio. Una caja de acero puede troquelarse o mecanizarse y acabarse en cuestión de horas, tal vez unos pocos días si se hace totalmente a mano. Un componente cerámico, independientemente de su tamaño y finalidad, tarda al menos dos semanas de principio a fin. Y digo un componente, no un reloj entero. En realidad, desde el acopio de materiales hasta el producto final, el tiempo medio de fabricación de un reloj Rado es de dos meses.
El mayor beneficio de este complejo proceso de fabricación es un material diferente a cualquier otro. Más ligero que el acero, pero mucho más duro y, por tanto, muy resistente a los arañazos. En la escala Vickers de dureza, la cerámica utilizada por Rado alcanza los 1.250 puntos, mientras que el acero inoxidable 316L alcanza los 152 puntos. Incluso el acero inoxidable 904L más denso utilizado por Rolex no supera los 500 puntos en la escala Vickers.
Todo empieza con polvo de óxido de circonio, que se mezcla con una serie de pigmentos coloreados y un aglutinante polimérico. Esta materia prima se funde y se inyecta a alta presión en un molde de precisión.
Estos moldes son increíblemente complejos, ya que tienen que tener en cuenta la contracción del material en pasos posteriores del proceso, y también deben incluir estructuras de soporte y canales de flujo para conseguir una pieza perfectamente moldeada.
Aquí se puede ver cómo empieza una caja y como, tras esos procesos termina en su tamaño final:
El siguiente paso es el proceso de desaglomerado, en el que se retira el aglutinante polimérico de las piezas cerámicas, preparándolas para la sinterización. Los componentes se introducen en un horno a 1.450°C y tardan una semana entera. La temperatura varía ligeramente en función del color de los pigmentos añadidos a la materia prima. Este proceso de sinterización reduce el tamaño de las piezas cerámicas en un 23% aproximadamente.
El truco está en hacer todos los cálculos de antemano, para conseguir la perfección después de la sinterización. Para hacernos una idea de la precisión necesaria, digamos que incluso se tienen en cuenta las roscas de los tornillos, que se moldean directamente en la carcasa.
Tras el proceso de sinterización, los componentes están listos para su acabado. Como lo único que puede afectar a la cerámica de alta tecnología es la propia cerámica de alta tecnología o algo aún más duro, cada componente se coloca en una cuba con granos de cerámica. Una vez allí, la cuba vibra y pule la superficie de los componentes. Este proceso puede durar hasta una semana, en función del resultado deseado, con varios pasos en los que se utilizan granos cerámicos de pulido cada vez más pequeños y, por último, simplemente polvo cerámico.
Las propiedades de la cerámica no son sólo técnicas, sino también estéticas. Es inmune a los arañazos, pero también totalmente hipoalergénica y puede acabarse con un pulido espejo o con un brillo mate. Rado confía tanto en su calidad que dispone de una estación de servicio in situ en su sede de Lengnau, donde se pueden ver con regularidad ejemplares antiguos en perfecto estado. Y es que un reloj de cerámica parece tan nuevo como el día que salió de fábrica, a pesar de su edad. Sin arañazos, ni golpes, ni imperfecciones, nada. Lo único que no se debe hacer es dejarlo caer desde una gran altura, ya que se rompería la cerámica. Si eso no ocurre, un Rado durará toda la vida como el primer día.
Una pequeña nota sobre los colores en cerámica: dado su proceso de fabricación, el color se ve al final del proceso. Es decir, al principio el color no se distingue. Es tras pasar por los distintos momentos en el que acaba por aflorar el color que se desea. Conseguir un color es fácil, ya se sabe qué pigmentos usar. Lo difícil es que TODOS los relojes de un color sean iguales. Que todos tengan el mismo Pantone, por así decir. En eso es en lo que Rado es un maestro.
Por otro lado, el color más difícil de conseguir es el rojo vivo, simplemente porque los pigmentos necesarios se queman antes que los demás, dando como resultado un tono más apagado que no resulta tan atractivo. Cierto es que Hublot presentó un Big Bang para el que decía que había creado una nueva tecnología para conseguir un rojo brillante (lo vimos aquí en vivo), pero el hecho es que, en realidad, no se sabe cuántos ha fabricado y, aunque era una serie limitada y se lanzó hace casi 7 años, aún está en el catálogo (y se vende bajo pedido). No sé, da que pensar, ¿verdad?.
Rado, por su parte, se está acercando a conseguirlo, pero por ahora son grados de naranja. Por ejemplo este Captain Cook con una inserción de cerámica en el bisel, que se aproxima bastante al ideal:
UN PASO MÁS ALLÁ: RADO PLASMA HIGH-TECH CERAMIC
Pero la historia de Rado y la cerámica no acaba aquí. A través de relojes como el Captain Cook Diver y el True Thin Line, hemos conocido los distintos tipos de color que Rado puede ofrecer, con un acabado mate o pulido. Sin embargo, hay un tipo de acabado aún más especial que se realiza en ComaDur, sólo para Rado: Plasma High-Tech Ceramic.
El Plasma High-Tech Ceramic no se parece a ningún otro material conocido. Se parte de componentes cerámicos pulidos de color blanco que se introducen en un reactor de plasma especial y se calientan hasta 20.000 °C.
Para poner las cosas en perspectiva: se calcula que el núcleo de la Tierra está a unos 5.200 °C e incluso la superficie del Sol alcanza «sólo» los 5.600 °C. Así que ver cómo un componente cerámico blanco fabricado por el hombre se dispara hasta los 20.000 °C y sale al exterior es como asistir al nacimiento de una estrella.
El proceso cambia estructuralmente el material y le da un aspecto de metal líquido. Sigue siendo resistente a los arañazos e hipoalergénico, pero el material ha cambiado en su esencia. Al tacto, es perfectamente liso y bastante ligero (entre el acero inoxidable y el titanio).
Para llevar a cabo este proceso hay un horno especial en una zona apartada de la fábrica en la que sólo está el horno. Dentro se disponen las piezas alrededor de la boca de la llama, que se dispara en vertical.
El horno tiene una pequeña ventana por la que se puede ver el proceso, que da una imagen muy de ciencia ficción:
El aspecto final de las cajas es metálico, pero con todas las características de la cerámica, no del metal. Y el que sea exclusivo de Rado le da una mayor exclusividad que si lo viéramos en las demás marcas del Grupo Swatch. Un ejemplo es el RADO Captain Cook que vimos en vivo, aunque a mí el que más me gusta es la referencia R32130312:
Por supuesto, después de la fabricación de la caja y el brazalete vienen los procesos habituales: montaje de la esfera, del calibre, control de hermeticidad y precisión… Todo con el nivel que se le exige a una marca así. Por eso ofrecen una garantía de 5 años. Y, por eso mismo, aunque los precios son más altos que los de modelos equivalentes de otras marcas, Rado tiene éxito porque el usuario reconoce la singularidad de los materiales y la calidad del conjunto.
En mi caso, presenciar todo el proceso de principio a fin, desde el polvo hasta la pieza acabada, fue algo increíble. Demuestra la dedicación de Rado a la relojería y al avance continuo en la investigación de materiales.
Y, como siempre digo, si alguna vez tienes la oportunidad de probarte un Rado, hazlo. De verdad. Te impresionará su aspecto y tacto, por no hablar de su precisión y calidad. Y más aún sabiendo todo lo que hay detrás de cada pieza.
Más información en Rado.es.